GLULAM
Composed of layers of timber bonded together with high-strength adhesive to create beams and columns that offer both structural support and architectural design flexibility.
Glulam, or glued laminated timber, is an engineered wood product made by bonding together layers of wood with adhesives.
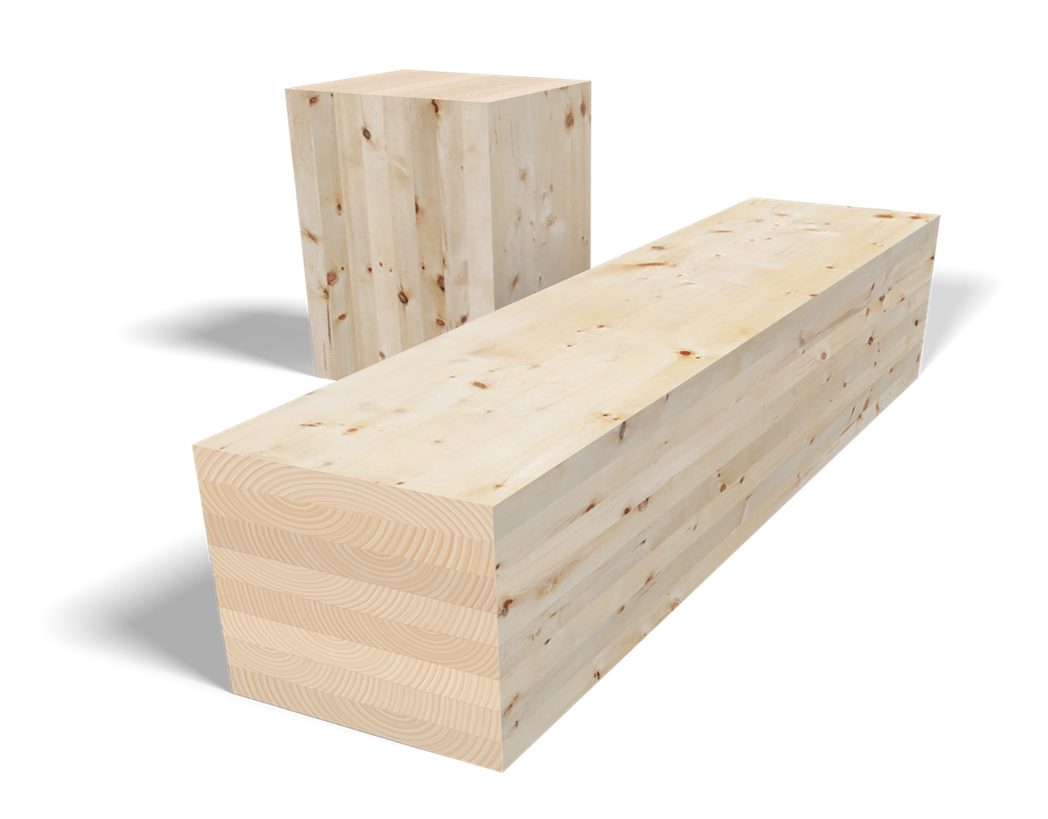
WHATS IS GLULAM ?
Glulam, or glued laminated timber, is an engineered wood product made by bonding together layers of wood with adhesives.
Here’s a breakdown of what you need to know
Composition and Production Layers
Glulam consists of multiple layers (or "laminates") of dimensional lumber that are glued together. Each layer is typically made from smaller pieces of wood, which are oriented with the grain running parallel to the length of the beam.
Adhesives
Strong, durable adhesives are used to bond the layers. These adhesives are often resins or other synthetic compounds designed to withstand structural loads.
Manufacturing Process
The layers of wood are glued together in a controlled environment, often under heat and pressure to ensure a strong bond. The laminated layers are then cut and shaped into various forms, such as beams, columns, or arches.
Strength and Flexibility
Glulam is strong and can be designed to carry heavy loads, making it suitable for large-span structures like bridges, roofs, and walls. It also offers flexibility in design because it can be curved or shaped to fit specific architectural needs.
Sustainability
Made from renewable resources, glulam is considered an environmentally friendly option compared to some other construction materials. It also has a lower carbon footprint compared to steel or concrete.
Consistency
Since the wood is engineered and layered, glulam typically has fewer defects like knots compared to solid wood, resulting in more consistent strength and stability.
Applications
Architectural Design: Used in both residential and commercial projects, glulam is popular for its aesthetic appeal and the ability to create large, open spaces without the need for many supports.
Structural Uses
Commonly used in the construction of beams, columns, arches, and even whole building frames. It’s ideal for applications where large spans or unusual shapes are required.
Considerations
Cost: Glulam can be more expensive than traditional lumber, but its strength and design flexibility often justify the investment.
Maintenance
It’s generally low-maintenance but should be protected from moisture and insects, as these can affect the adhesive and the wood.
WHY GLULAM ?
Glulam, or glued laminated timber, offers several advantages that make it a compelling choice for various construction and architectural applications.
Here are some key reasons why glulam is often chosen
Strength and Load-Bearing Capacity
High Strength-to-Weight Ratio: Glulam beams and columns can handle substantial loads while being relatively lightweight compared to materials like concrete or steel.
Large Spans: It is capable of spanning long distances without the need for intermediate supports, making it ideal for large open spaces such as auditoriums and sports halls.
Design Flexibility
Custom Shapes: Glulam can be fabricated into a variety of shapes, including curves and arches, which can be challenging or impossible with solid wood or other materials.
Architectural Aesthetics: It offers a natural wood appearance that can be visually appealing in both traditional and contemporary designs. It also allows for creative architectural solutions.
Sustainability
Renewable Resource: Made from wood, which is a renewable resource, glulam contributes to more sustainable construction practices compared to materials like steel or concrete.
Carbon Sequestration: Wood naturally stores carbon dioxide, which can help offset carbon emissions over the lifecycle of the building.
Consistency and Durability
Uniform Quality: The manufacturing process reduces the presence of natural defects like knots and splits, resulting in a more consistent and reliable material.
Durability: When properly treated and maintained, glulam is durable and resistant to issues like warping or shrinking that can affect solid wood.
Efficiency and Cost-Effectiveness
Efficient Use of Resources: By using smaller pieces of wood, glulam makes efficient use of timber resources, potentially reducing waste.
Reduced Construction Time: Pre-fabricated glulam elements can speed up construction time because they arrive on-site ready to install, reducing labor and on-site construction time.
Performance in Fire and Seismic Events
Fire Resistance: Glulam performs well in fire situations because it chars on the outside but maintains strength internally. This can provide valuable time for evacuation and firefighting.
Seismic Resilience: It can be engineered to perform well in seismic conditions, offering flexibility and strength in areas prone to earthquakes.
Low Maintenance
Ease of Care: Glulam structures typically require less maintenance compared to some other materials, especially if they are properly treated and protected from the elements.
In summary, glulam offers a combination of structural strength, design versatility, sustainability, and aesthetic appeal, making it an attractive choice for a wide range of construction projects.
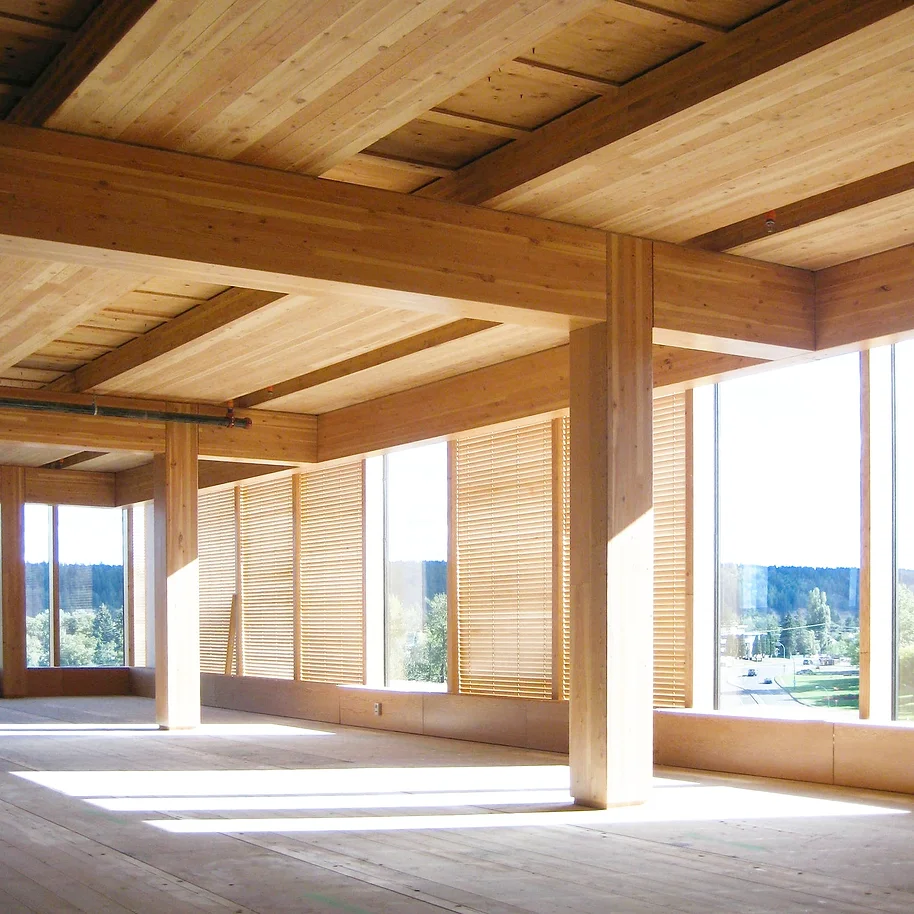
Glulam and its range of use
Whilst Glulam is often first choice for environmental and aesthetic reasons, it’s also popular for its versatility. You can use Glulam in almost any type of structure; we’ve named a few examples below for your interest, information, and inspiration.
- Arenas
- Balcony roofing
- Cambered beams
- Conference halls
- Decking
- Floorboards & beams
- Garages
- Halls & arched beams
- Homes
- Joist
- Lintels
- Pillars & columns
- Roof beams
- Rafters
- Load - bearing beams
- Schools
- Sheds
- Shopping centres
- Station supports
- Trusses
- Walls
CAPACITY
In our facilities, we excel in producing a wide range of customizable glulam options. Our skilled production team is adept at crafting glulam beams with custom lengths and thicknesses to meet your unique project requirements.
GLULAM DIMENSONS
Straight Members Length up to 12m | THICKNESS (mm) | |||||
90 | 135 | 180 | 225 | 270 | 315 | |
200 | ✓ | ✓ | ✓ | ✓ | ✓ | ✓ |
250 | ✓ | ✓ | ✓ | ✓ | ✓ | ✓ |
300 | ✓ | ✓ | ✓ | ✓ | ✓ | ✓ |
350 | ✓ | ✓ | ✓ | ✓ | ✓ | ✓ |
400 | ... | ... | ... | ... | ... | ... |
WIDTH (mm) | ✓ Standard cross-sections | … Special Order |
Lenght: 12
|
Thickness x Width (m)
|
---|---|
![]() |
0,18 X 0,2
|
![]() |
0,18 X 0,25
|
![]() |
0,18 X 0,30
|
![]() |
0,18 X 0,35
|
![]() |
0,225 X 0,2
|
![]() |
0,225 X 0,25
|
![]() |
0,225 X 0,30
|
![]() |
0,225 X 0,35
|
Lenght: 12
|
Thickness x Width (m)
|
---|---|
![]() |
0,27 X 0,2
|
![]() |
0,27 X 0,25
|
![]() |
0,27 X 0,30
|
![]() |
0,27 X 0,35
|
![]() |
0,315 X 0,2
|
![]() |
0,315 X 0,25
|
![]() |
0,315 X 0,30
|
![]() |
0,315 X 0,35
|